Definition of the DOD Corrosion Problem
The DOD corrosion problem is quite complex. Scientists and engineers incorporate corrosion control into the design process, construction, and maintenance procedures from project conception to ultimate disposal.
In spite of these efforts, corrosion is a very serious problem. The photograph below illustrates a heavily corroded piece of DOD equipment. This piece of equipment is almost new.
Another photograph of the same piece of equipment is presented on the following page. This piece of equipment had been designed, constructed, and maintained according to DOD specifications, yet it is still heavily corroded.
This piece of equipment is very difficult to maintain. Most of the fasteners are frozen. This means that simple maintenance or repair procedure may take hours as the mechanics wait for non-ICC penetrants to take effect, or even worse, deal with broken fasteners and parts.
Because the corrosion problem is permanent, the corrosion control solution should also be permanent. This means that an effective corrosion control procedure must be implemented for the entire lifetime of the equipment.
For this reason, it is necessary to have a permanent corrosion control procedure in place that requires little to no surface preparation, that uses inexpensive materials, that requires a minimal amount of time and effort to apply, and has no adverse effect upon the reliability, lifetime, or operation of the treated equipment.
The scale of the DOD losses to corrosion is enormous. 20 billion dollars a year[1].
According to the Federal Highway Administration study the indirect losses to corrosion are similar to the direct losses. This means that an estimated 40 billion dollars a year are lost to corrosion. This is almost ten percent of the entire DoD budget. The same funds could be more effectively allocated to personnel and procurement.
This cost does not take into account the morale issues associated with corrosion, nor does it take into account the injuries and deaths associated with equipment and weapons failures caused by corrosion.
Paths to Reducing Corrosion Losses
There are three primary paths to reducing corrosion losses:
- Improved materials – The design and evaluation process may take years. The cost of the replacement materials may be much higher than the original item. This approach does not have a significant positive impact on equipment in the field.
- Improved coatings – The verification of the improved efficacy of the improved coating may take years. The cost of the new coating may be much higher than the coating it replaced. The application of the new coating requires significant surface preparation and equipment downtime. The new coating will only improve the efficacy of the newly coated equipment.
- Improved corrosion inhibitors – immediate results, low cost, and universal applicability Corrosion inhibitors have the benefits of the ability to generate immediate results, the lack of a need for surface preparation, low cost, and the ability to deal with corrosion on all types of equipment
Historical Drawbacks of Corrosion Inhibitors
Corrosion inhibitors have a major problem: in most situations they are not effective based upon the following problems:
- Short film life – Corrosion inhibitors often evaporate within days or weeks of application. This phenomenon applies to most multi-purpose corrosion inhibitors, i.e. corrosion inhibitors that also function as penetrants and lubricants. Side-by-side testing has indicated that in many cases there is a negligible difference between the performance of a multi-purpose corrosion inhibitor and an untreated surface.
An example of a corrosion inhibitor failure based upon evaporation is presented below.
Note the TC-11 plate on the right shows no sign of corrosion
after exposure alongside the plate on the left.
Wax films – this type of corrosion inhibitor is effective for long-term storage, but it is not effective for operational equipment other than the treatment of voids. The wax film builds up and interferes with the operation of articulated mechanisms. In many cases it is necessary to use a hazardous solvent to remove the wax film prior to operating the equipment. Wax film corrosion inhibitors have a negligible penetrating capability. The wax film corrosion inhibitor is mobile for a few minutes after application, but once the carrier solvent evaporates the wax film will not penetrate into cracks and crevices.
Side-by-side testing has indicated that corrosion can occur underneath an intact wax film, as presented below.
Note the left plate example of a Wax Based Corrosion
Inhibitor Failure with A Robust Wax Film in Place
and the pristine example of a plate treated with TC-11
and exposed to the same environment as the Wax Based treatment.
Many corrosion inhibitors have severe compatibility issues. The corrosion inhibitor causes elastomers to shrink or expand, either of which can lead to component failure. Some corrosion inhibitors actually cause plastic to melt on contact.
Compatibility testing tends to focus on the effects of short-term immersion in a corrosion inhibitor rather than the long-term effects associated with an elastomer being coated with a corrosion inhibitor. ICC has used an approach to evaluating compatibility that focuses on long-term effects of an elastomer being coated with a corrosion inhibitor, since this approach is more representative of real world conditions.
The compatibly of corrosion inhibitors has decreased as manufacturers have incorporated non-volatile solvents such as Isopar L, M, and J into their formulations in order to comply with restrictions on the volatile organic constituent content of their product imposed by regulatory agencies. These solvents have serious long-term compatibility issues.
Some corrosion inhibitor manufacturers do not provide test data to support their product claims. This is a serious drawback that his limited the use of corrosion inhibitors in the field. Many customers are not satisfied with the performance of corrosion inhibitors because in some cases the manufacturer has failed to quantify the performance of their corrosion inhibitor in specific situations.
None of these issues affect the H&N Industries, LLC product line.
Characteristics of TC-11 Corrosion Inhibitors
- Minimal surface preparation required – no special effort should be required to clean the item to be protected other than, if necessary, to wash down the item to remove heavy deposits of dirt or mud.
- Long film life – the corrosion inhibiting film should last long enough to encourage end users to utilize the product. If the product fails in a short amount of time end-users will avoid the product.
- Non-hardening – the corrosion inhibitor should not generate a wax film that interferes with the operation of articulated mechanisms or is difficult to remove.
- Waterproof – the corrosion inhibitor should be impervious to water, even if the item to be protected is completely submerged for extended periods of time
- Resistant to salt – the corrosion inhibitor should not be affected by salt. This characteristic becomes more important as a salt-water droplet evaporates and the salinity approaches 100%. This is the most common source of corrosion inhibitor failure.
- Resistant to sunlight – the corrosion inhibitor should be resistant to sunlight for a month or more.
- Strong penetrating effect – the corrosion inhibitor should be able to penetrate into fastener threads, cracks, and crevices over the entire lifetime of the film. Ideally the corrosion inhibitor will break the bond between corrosion particles and the underlying metal, thereby un-freezing the fastener or part.
- Excellent lubricating qualities – the corrosion inhibitor should provide long-term lubrication. Ideally the corrosion inhibitor will be able to resist high rotational speeds and high loads.
- Eliminate galvanic action – the corrosion inhibitor should stop galvanic action between dissimilar metals for the lifetime of the film, even if the item is inundated..
- Self-healing – if the corrosion inhibitor film is displaced by abrasion, the film should be self-healing.
- Easy to remove – it should be possible to remove the corrosion inhibitor with an environmentally friendly cleaner.
- Complete compatibility with all types of rubber, paint, and plastic – the corrosion inhibitor should not adversely affect any rubber, paint, or plastic used in the construction of the item to be protected.
- Low cost – the cost of the corrosion inhibitor should be low enough to allow for a high cost benefit ratio.
- Minimal environmental impact – the corrosion inhibitor should comply with all existing and proposed environmental regulations.
The Advanced TC-11 Corrosion Inhibitors meet all of these criteria.
Optimal Applications for Advanced Corrosion Inhibitors
- Equipment shipped as deck cargo – equipment shipped as deck cargo should arrive at its final destination in the same condition that it was in when it left its point of origin. This seems obvious, but it is very difficult to implement.
- Weapons – weapons should not corrode in the field. Cosmoline is a highly effective product for long-term storage, but in many cases once a weapon is put into operation corrosion is a serious issue. Weapons should be completely corrosion free, even if they have been submerged. The corrosion inhibitor should have no effect on the materials and coatings on the weapon.
- Electromechanical systems – equipment should maintain the same level of functionality and appearance for the entire lifetime of the item, even if the equipment is used and stored in a harsh environment.
Equipment Shipped as Deck Cargo
TC-11 has five years experience in delivering deck cargo that is in exactly the same condition when it arrives at its final destination that it was at the point of origin. This is in spite of the fact that the equipment is shipped as deck cargo on an open barge in the roughest conditions in the World: the North Pacific Ocean in the middle of winter when wave heights of 40 feet are not uncommon. The waves break over the bow of the barge and generate a salt mist that penetrates every item on the barge. The conditions are so corrosive that a paint film will fail in a matter of days.
The vast majority of the Caterpillar, International, Case, John Deere, Volvo, Komatsu and other heavy equipment shipped from the West Coast to destinations throughout the Pacific have been treated with TC-11 Corrosion Inhibitor since July of 2001. The entire piece of equipment is treated with TC-11 for a cost of less than $15 per lineal foot. During this time there has not been a single incident of incompatibility with any of the rubber, paint, or plastic on any of the pieces of equipment treated.
A typical deck cargo is presented below. The conditions on this particular voyage were so rough that the tug failed and the normal 16-day voyage was extended to 27 days.
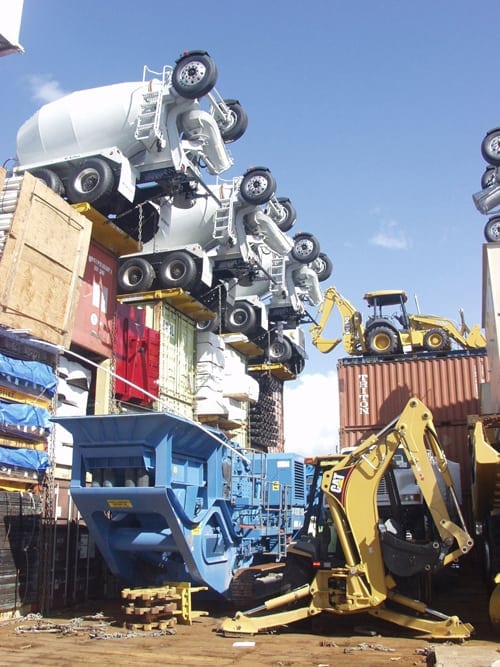
Typical Barge Deck
The blue paver on the left was one of the few pieces of equipment that was not treated with TC-11 Corrosion Inhibitor.
The photograph below demonstrates that the conditions were so corrosive that the paint film on the untreated paver failed.
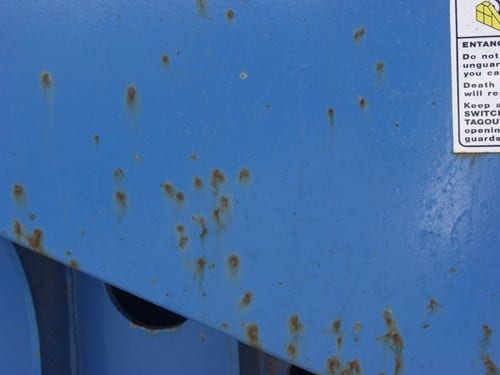
Untreated Surface of Equipment
The condition of a piece of equipment that was treated with TC-11 Corrosion Inhibitor is presented below.
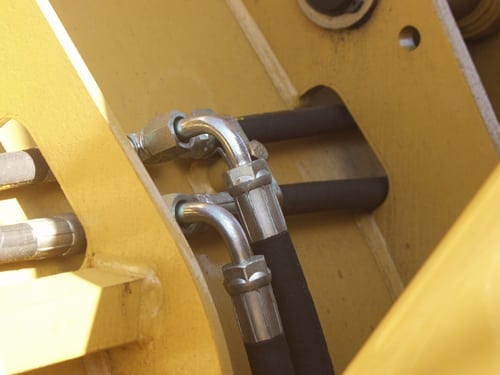
Surface treated with TC-11
The condition of an untreated engine is presented below
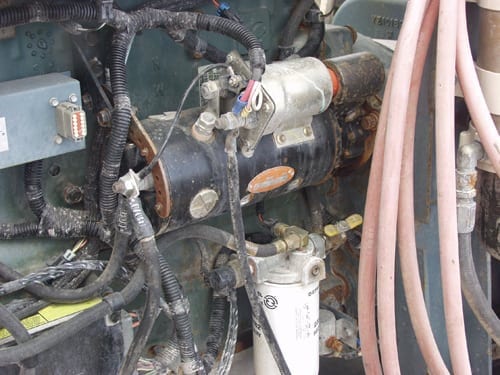
Untreated Engine
The condition of a treated engine is presented below:
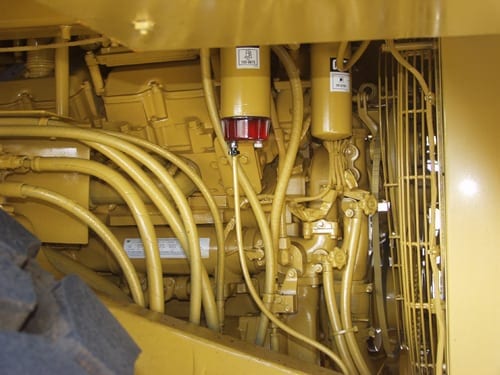
Engine treated with TC-11
The condition of an untreated component is presented below. Once again the paint film has failed during a relatively short exposure to highly corrosive conditions.
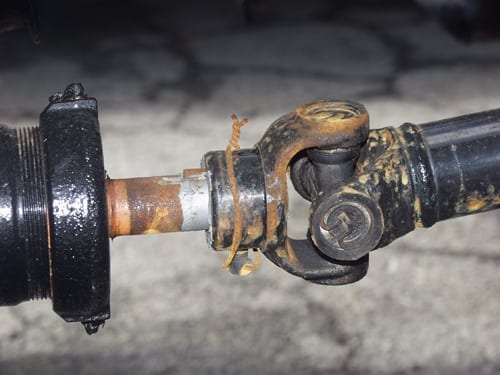
Untreated Universal Joint
The condition of a treated component is presented below
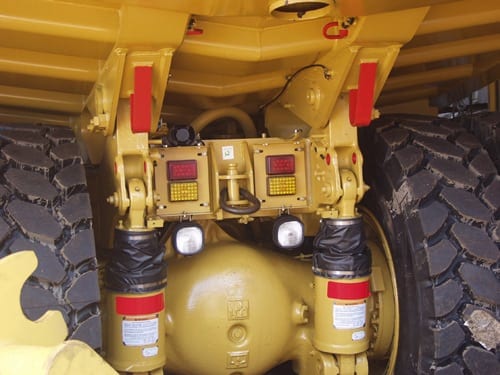
Suspension treated with TC-11
ICC Management feels very strongly that the DoD can immediately utilize TC-11 Corrosion Inhibitor for the protection of deck cargo based upon five years of successful experience with equipment that is similar in construction and value to DoD equipment.
Cables
ICC has developed a product that is specifically designed for the protection and lubrication of all types of cables – TC-11 Cable Coat©.
The TC-11 Corrosion Inhibitor formula was modified to eliminate the possibility of a sheen and to increase the lifetime of the film in a submerged environment.
A photograph of a steel panel treated with Cable Coat after ninety two days of immersion is presented below. The condition of a panel treated with a competing product and immersed for the same amount of time is presented for comparative purposes. This test is still underway with no signs of TC-11 Cable Coat film failure.
TC-11 Gun Cleaning
The unique characteristic of TC-11 is that it removes residue and corrosion as effectively or better than any competing product without affecting bluing, wood, paint, rubber or plastic parts. The importance of this characteristic cannot be overemphasized. Many gun-cleaning solvents have specific directions to avoid contact between the solvent and any portion of the weapon other than the area being cleaned. TC-11 has no effect on any material or coating used in the construction of a weapon.
A photograph of a gun cleaning patch treated with TC-11 after wiping a barrel cleaned with a leading competitor showing a large amount of residue removed and demonstrating the superior efficacy of TC-11 is presented below.
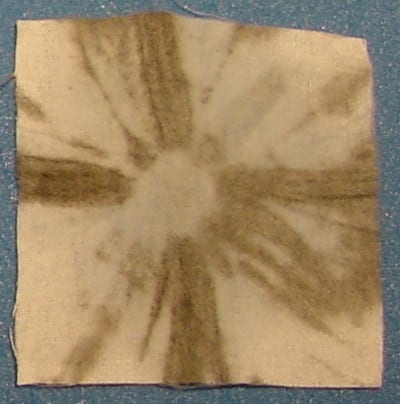
A photograph of a cleaning patch soaked with competing product used to wipe down barrel cleaned with TC-11 showing no residue removed from a gun barrel cleaned with TC-11
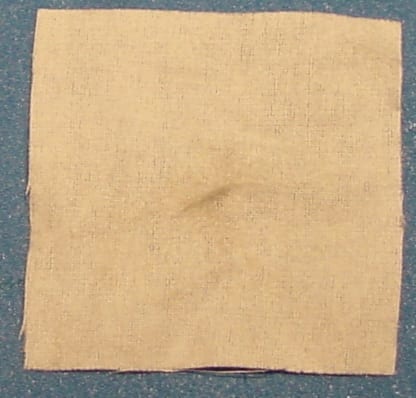
TC-11 has minimal health and safety issues and as well as a high cost benefit ratio.
TC-11 Ultimate Gun Protection
- TC-11 preserves weapons in the field to an unprecedented degree and it incorporates the following features.
- TC-11 is easy to apply – there is no need for special surface preparation. TC-11 can also be used to clean and lubricate weapons.
- TC-11 completely penetrates intricate mechanisms – this means that weapons are completely protected. TC-11 displaces any moisture that may be present.
- TC-11 protects weapons in the field to an unprecedented degree, even if the weapon is submerged. The micro-spaces in the threads and fittings will be filled with TC-11, so if the weapon is immersed the water will never come into contact with the weapon. TC-11 is even effective in salt water.
- TC-11 provides long-term corrosion protection and lubrication. TC-11 does not evaporate and it does not harden into a wax film.
- TC-11 is completely compatible with all materials of construction and coating.
- TC-11 has minimal safety and health issues as well as a high cost benefit ratio.
Electromechanical Systems
- TC-11 Corrosion Inhibitor is an optimized product for the preservation of electromechanical systems with a minimum of cost and effort.
- The film life of TC-11 is long enough to motivate end users to maintain a thin coat of TC-11 to prevent corrosion damage to electrical and mechanical components.
- TC-11 Corrosion Inhibitor prevents the corrosion of metallic parts, even if the equipment is used and stored in a salt environment.
- TC-11 Corrosion Inhibitor Makes electrical connectors and components waterproof. An engine treated with TC-11 will continue to run until water is ingested into the intake manifold.
- TC-11 Corrosion Inhibitor penetrates into intricate mechanisms. This means that throttle linkages continue to operate smoothly for the lifetime of the equipment and that components can be disassembled and re-assembled with a minimum of time and effort.
- TC-11 Corrosion Inhibitor lubricates articulated mechanisms.
- TC-11 Corrosion Inhibitor does not affect rubber, paint, and plastic.
- TC-11 Corrosion Inhibitor has a minimal environmental impact and a high cost benefit ratio.
A photograph of a new electromechanical component treated with TC-11 Corrosion Inhibitor is presented below.
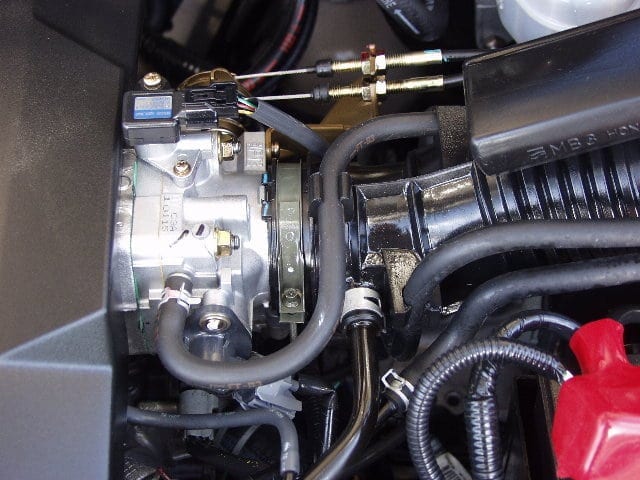
The glossiness of the rubber and plastic parts is an indication that a heavy coat of TC-11 Corrosion inhibitor was applied to the parts in order to study the compatibility of the part with long-term exposure to TC-11 Corrosion Inhibitor.
A photograph of the same component after five years of operation and storage in a salt laden environment is presented below.
MISSING PHOTO
All of the metal parts are completely corrosion free. All of the moving parts are unaffected by five years of operation. All of the rubber and plastic parts are unaffected by five years of exposure to heat and ozone. The appearance and the functionality of the component is “like new”.
An added benefit is that the components are completely waterproof. If the engine compartment is inundated by operations or cleaning the electrical systems are unaffected.
It is interesting to compare the condition of this treated unpainted component with the condition of a painted component that was not treated with TC-11 Corrosion Inhibitor. The environmental exposure for the two items was virtually identical, the only difference being that one item was treated with TC-11 Corrosion Inhibitor and the other item wasn’t.
The salient feature of TC-11 Corrosion Inhibitor is that the cost of protecting the entire piece of equipment requires less than $100 worth of material and labor a year. It seems reasonable that the difference in the functionality and appearance of a treated and an untreated piece of equipment is worth significantly more than $100 per year.
ICC Management firmly believes that the DoD can save millions of dollars a year with a minimum of cost and effort by incorporating this well proven corrosion control concept into DoD maintenance and repair procedures.
Test Programs
TC-11 has invested significant time and effort in generating test results to substantiate product claims. These test programs include:
Side-by-Side Corrosion Testing
- Side-by-Side Compatibility Testing
- Side-by Side Penetration Testing
- Side-by-Side corrosion Testing
The objective of the Side-by-Side Corrosion testing was to provide comprehensive qualitative test data that compared the corrosion control performance of TC-11®Corrosion Inhibitor to all other corrosion control products on the market and to generate estimates of the TC-11 Corrosion Inhibitor film life in various environments.
The Side-by-Side Corrosion Test procedure is presented below.
- Factory sealed ground finish steel Q-panels are removed from their package and are wiped down with acetone to remove the corrosion inhibitor applied by the manufacturer.
- The Q-panel is treated once with a bulk lubricant.
- The Q-panel is mounted on a rack with all of the other Q-panels.
- The Q-panel is exposed to full sunlight, rainfall, and a condensation cycle.
- The Q panel is photographed at 12-hour intervals with a high-resolution digital camera.
- The lab color histogram function of Adobe Photoshop® 7 is used to count the number of rust colored pixels on each panel.
- The pixel counts are converted to the percentage of the Q-panel surface area covered with corrosion.
- The product is graded according to the average percentage of the Q-panel covered with corrosion during the 60-day test period.